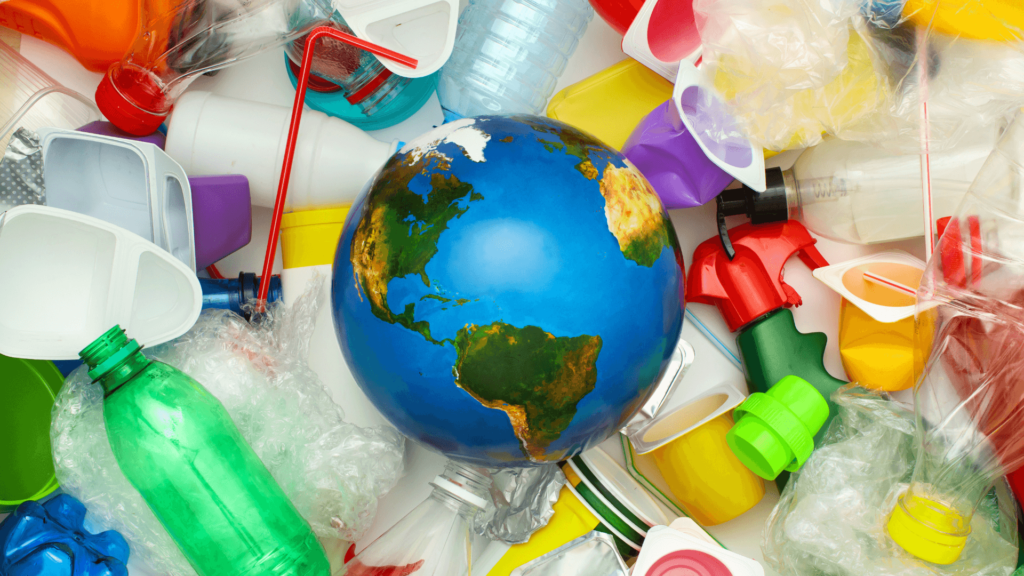
R&D hiring challenges for BPA alternatives
As regulatory pressures and consumer demand push the plastics industry toward safer and more sustainable materials, companies are investing in research and development (R&D) to find alternatives to Bisphenol A (BPA). However, recruiting and retaining the right talent for this specialised field presents significant challenges. Addressing these requires a strategic approach to workforce planning, skills development, and cross-disciplinary collaboration.
Key Skills Required in BPA Alternative R&D
Developing BPA alternatives requires expertise in multiple scientific and engineering disciplines, including:
- Material Science and Polymer Chemistry – Experts in these fields are essential for developing and testing new plastic formulations.
- Toxicology and Environmental Science – Ensuring new materials meet safety and environmental regulations requires professionals skilled in chemical risk assessment.
- Chemical Engineering – Process engineers help scale laboratory innovations to commercial production.
- Regulatory Affairs and Compliance – Specialists in global chemical regulations (e.g., REACH, FDA, EPA) ensure new materials align with evolving legal frameworks.
- Sustainability and Circular Economy Experts – Companies increasingly seek professionals who can integrate recyclability and sustainability into product design.
Recruitment Challenges
- Shortage of Specialised Talent – The pool of experts in alternative polymer development is limited, making it difficult to find professionals with the necessary skills.
- Competition Across Industries – Chemical and material science professionals are in demand across multiple industries, including pharmaceuticals, energy, and electronics, creating strong competition for talent.
- Evolving Regulatory Landscape – Companies require specialists who can navigate complex and shifting regulations, but this expertise is often scarce.
- Bridging Science and Business Needs – While R&D teams focus on technical development, companies also need professionals who understand commercialisation, market trends, and consumer preferences.
- Workforce Retention and Upskilling – Retaining top talent requires investment in continuous learning and development, especially as new scientific discoveries and regulatory changes emerge.
Addressing Talent Gaps
The Role of Specialised Recruitment Firms
Given the niche skill set required for BPA alternative R&D, specialised recruitment companies can play a crucial role in bridging talent gaps. These organisations offer:
- Access to a Niche Talent Pool – Specialised recruiters have extensive networks within material science, chemical engineering, and sustainability sectors, making it easier to identify qualified candidates.
- Industry-Specific Expertise – Recruiters with deep knowledge of the plastics and chemical industries can effectively match companies with professionals who possess both technical and regulatory expertise.
- Faster Hiring Processes – Leveraging their industry connections, recruitment firms can significantly reduce the time it takes to find and onboard top talent.
- Market Intelligence and Competitive Insights – Recruitment companies provide valuable data on salary trends, hiring challenges, and evolving industry demands, helping companies refine their talent acquisition strategies.
- Support for Workforce Planning and Upskilling – Some recruitment companies offer advisory services to help businesses develop long-term workforce strategies, including reskilling initiatives and succession planning.
- Industry-Academic Partnerships – Collaborating with universities can help develop a pipeline of emerging talent through research projects, internships, and specialised degree programmes.
- Upskilling Existing Workforce – Offering training in material innovation, sustainability, and regulatory compliance helps current employees transition into specialised roles.
- Expanding Recruitment Strategies – Looking beyond traditional talent pools and recruiting professionals from adjacent industries (e.g., biotech, pharmaceuticals) can help bridge skill gaps.
- Investment in AI and Automation – Leveraging AI-driven material discovery and automation can reduce dependency on highly specialised R&D personnel.
Companies Investing in BPA Alternatives
Several companies and organisations are actively engaged in researching and developing alternatives to BPA. Notable efforts include:
- Eastman Chemical Company – Developed Tritan™, a copolyester designed as an alternative to BPA-containing polycarbonate plastics.
- Bayer AG, Kumho P&B Chemicals Inc., and LG Chem – Focused on developing bio-based or BPA-free plastics to meet consumer and regulatory demands.
- European Chemicals Agency (ECHA) – Launched projects like ‘SNA-BPA’ to support companies in substituting bisphenols in various applications.
- U.S. Environmental Protection Agency (EPA) – Evaluated alternative chemicals for thermal paper used in receipts to replace BPA-based coatings.
These initiatives highlight the growing efforts across industries and regulatory bodies to identify and implement safer alternatives to BPA, addressing both consumer health concerns and regulatory requirements.
We can see that the shift away from BPA presents both an innovation opportunity and a talent challenge. Companies that proactively invest in workforce development, strategic recruitment, and interdisciplinary collaboration will be best positioned to lead in BPA-free material development. A strong talent strategy, coupled with technological advancements, will be essential in creating safe, sustainable, and market-ready alternatives.
By James Connelly, Senior Manager, Chemicals, Skills Alliance